Each construction project comes with its own set of challenges. Every site, building, client, and project team is unique, and should be treated as such. With over 30,000 multi-family units constructed, we’ve found that it is essential to set expectations and quality standards up front.
It’s one thing to see your building design on paper or a computer screen, but it’s entirely different when you see an actual model of the finished product. Here are two practices we routinely deploy that can make a major difference in the final quality of your projects.
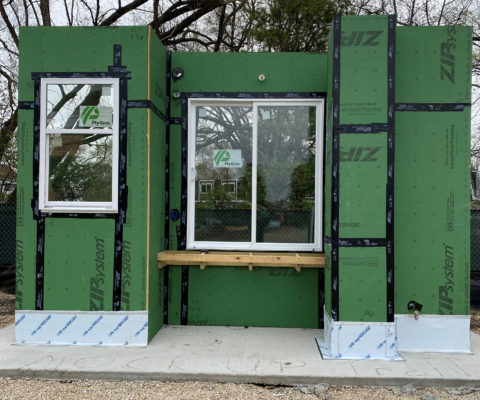
#1. Mock-Up Wall
We construct a freestanding mock-up wall mimicking the building façade with a standard window, patio door, and each façade material, transition, and flashing condition.
Our clients, architects, and manufacturer representatives review the installation of the products to ensure they meet all aesthetic and warranty requirements.
Focusing on the most critical components of a building’s envelope, the mock-up wall helps resolve coordination issues and future RFIs to drive our building enclosure schedule and ensures a quality envelope installation for years to come. Partnered with product manufacturers, subcontractors, building designers and our own quality assurance team, we review every detail to ensure the ultimate performance of our buildings.
We’ve found this process strengthens our relationship with both our clients and our trade partners. It’s a tested and distinctive method to provide an efficient and quality construction process from groundbreaking to ribbon cutting.
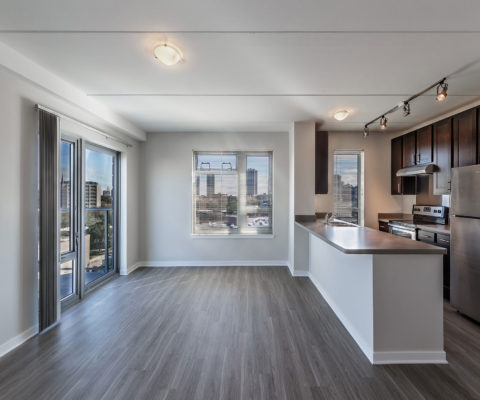
#2. Mock-Up Unit
We expedite construction in one unit to serve as a mock-up. Our team schedules reviews with the entire project team – including developers, property managers, architects, and trade partners – at multiple stages of the buildout and once the unit is “turnover ready.”
This sets clear standards for the turnover process, eliminates surprises, and mitigates mass-scale issues that can be resolved up front. This also allows our clients to identify any changes they may want to make in advance of all units being completed and minimizes re-work and change orders.
Our mock-up process is something we take a lot of pride in – it helps foster open communication and encourages a proactive approach to issue resolution. Ninety-five-percent of a project’s success is accomplished in the pre-construction process, and that is where McShane makes its biggest impact.